汽车壳体(新能源汽车电池包箱体结构的轻量化研究现状)
Posted
篇首语:书到用时方恨少,事非经过不知难。本文由小常识网(cha138.com)小编为大家整理,主要介绍了汽车壳体(新能源汽车电池包箱体结构的轻量化研究现状)相关的知识,希望对你有一定的参考价值。
汽车壳体(新能源汽车电池包箱体结构的轻量化研究现状)
电动汽车动力系统是一个机械和电气相结合的复杂结构体,设计时应充分考虑其刚度、强度、振动及使用寿命。随着电动汽车对高能量密度和短时间充电的迫切需求,三元正极材料、快速充电技术的应用使锂离子电池极易发生机械滥用、电气滥用和热滥用,进而导致电池系统热失控和整车起火爆炸,故动力锂离子电池已成为新能源汽车动力系统领域研究的热点和难点。电池包箱体(壳体)是电池包的主要承载部件,只有箱体的静、动态(刚强度、模态等)稳定,才能保证动力电池不出现滥用工况,使动力系统平稳运行。本文针对新能源汽车电池包箱体轻量化途径(材料选择、结构设计和制造技术)的研究成果进行系统梳理,对主流电池包箱体轻量化技术进行阐述,并分析其研究重点和发展方向。
2
电池包箱体材料轻量化研究进展
电池包箱体材料应具备电绝缘性、高散热性和化学稳定性等特点,箱体一般由上、下箱体和密封系统组成。电池包质量占整车系统质量的18%~30%,而箱体质量约占电池包总质量的10%~20%。目前普遍使用金属作为电池包箱体材料,复合材料由于其优异的比刚强度也逐渐受到重视。
2.1 电池包箱体用金属材料
在电池包箱体所用的金属材料中,钢板材料的制造工艺简单、成本低,具有较好的导热性、抗冲击性和热管理能力,为箱体的常用材料,但其主要缺点是质量较大。随着汽车轻量化设计理念的深入,铝合金因密度小、刚强度大和压铸性能好等优点,逐渐成为实现汽车轻量化的主要材料,目前已经生产出铸铝电池箱、铝板材电池箱和铝型材电池箱等产品。其中,铝制电池包箱体的承载结构主要分为底板式和框架式。大众公司研究发现,框架承载式结构的箱体能满足不同结构的强度要求,更易实现轻量化。
此外,金属和塑料的结合也是实现电池包箱体轻量化的主要方式,如比亚迪-秦(Pro EV500)电池包的上、下壳体分别采用片状模塑料复合材料(Sheet MoldingCom⁃pound,SMC)和高强铝。考虑到成本、加工等因素,国内入门级和经济型电动汽车的电池包外壳多采用钢制箱体,部分新能源汽车电池包采用金属箱体材料,如表1所示。
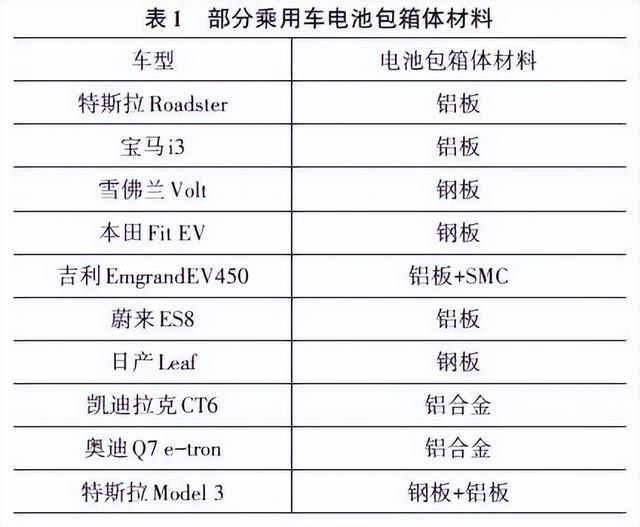
2.2 电池包箱体复合材料
电池包箱体使用的复合材料以碳纤维复合材料、玻璃纤维增强复合材料和 SMC复合材料等轻量化材料为主,不同材料制成的电池包箱体结构如图1所示,国内外学者对复合材料箱体也有针对性的研究。如Baumeister等利用泡沫铝复合三明治材料成功制成了能转载20 kW·h 的电池包下壳体,并使下壳体质量减轻了10%~20%。Choi等以尼龙6(PA6)为基体,通过改变碳纤维和玻璃纤维的含量(纤维总掺加量不超过40%),在满足强度、冲击等性能的条件下,成功开发出相比普通钢材质量减轻31%的增强塑料下壳体。毛占稳等与一汽轿车共同开发碳纤维电池包箱体,成功将箱体质量由110 kg减轻到19 kg。
碳纤维增强复合材料具有密度低、刚强度大等优点,已在电池包箱体中大量应用。德国ICT化工技术研究所研制出了一种以聚氨酯为基体的热固性塑料电池包箱体,该箱体质量35 kg,可承载340 kg的电池组,比同等规格钢材质量减轻35%以上。邵明顶等利用连续玻璃纤维编织布作为基材,环氧乙烯基树脂作为基体的玻璃纤维增强复合材料通过预浸料模压成型工艺制作电池箱体,也实现了轻量化效果。
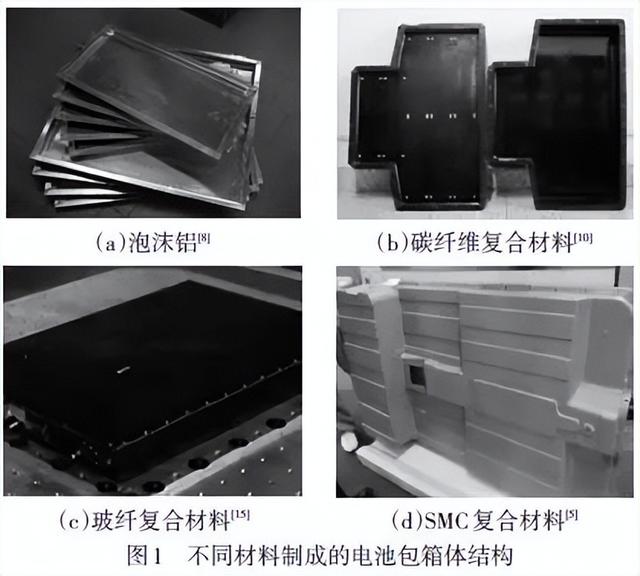
从上述国内外研究进展可以看出,电池包的轻量化研发和设计进程将会持续进行,但新材料、新工艺所带来的制造成本较高,并不利于大规模应用。新能源汽车动力电池包箱体设计需要综合考虑电池包的内部散热、防水防尘和安全性问题,所以兼顾动力电池包的轻量化和其他各项性能平衡的设计将会是一项重要的挑战。
3
电池包箱体结构轻量化研究
目前,新能源汽车电池包箱体多固定在汽车底板安装支架上,一般分为上、下壳体2个部分,结构如图2所示。
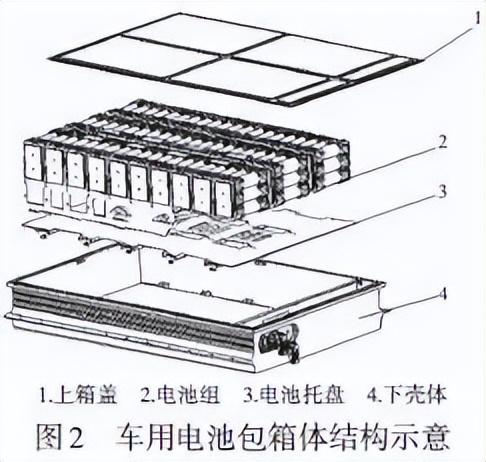
3.1 电池包形状及布置
目前新能源汽车的电池包结构主要有“土”字型、“凹”字型、“T”字型和“滑板”式,其形状和布置方式主要受车型开发平台的影响,不同电池包结构如图3所示。以图3b所示的“凹”字型电池包为例,电池包箱体的布置充分利用了汽车底板与地面之间的空间结构,使其能与乘员舱底板充分贴合,但上壳体靠近车身地板,地板部分结构也会与电池包箱体产生冲突,所以电池包布置时还应考虑与车身地板间的间隙等因素。在结构上对箱体所用冲压材料的厚度进行了相应减薄,并配合外部凸筋进行组装,简化了电池包结构特征,减轻了质量,提高了电池包的密封性和可靠性,但该电池组缺乏有效的电池热管理系统,会降低极端环境下的使用性能。
在电池包箱体结构设计中,图3d所示的“滑板”式电池包设计较为经典,电池包与车身底板融为一体,极大节约了使用的空间,且利用整车的框架对电池组进行保护,这种结构已成为电动汽车电池包设计的主要趋势。
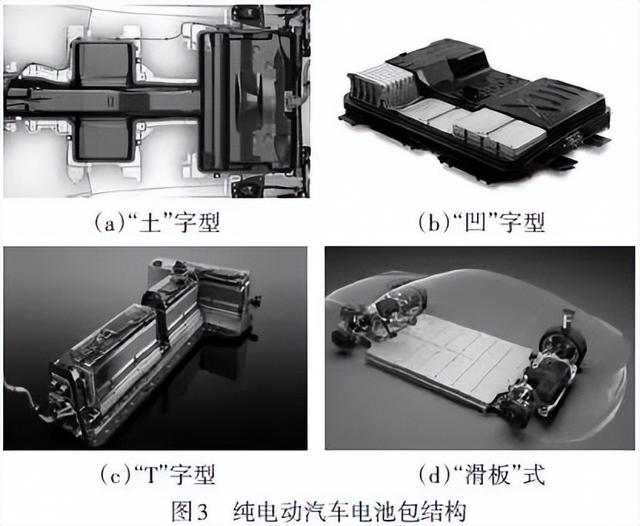
电动汽车电池包的布置方式需要根据汽车整体的空间结构和布局进行设计,离地间隙、驱动方式和载荷是需要考虑的重要因素。随着电池包技术的不断突破,其布置方式也更加科学合理,表2汇总了不同品牌车型的电池包排列方式,可以看出电池包的布置形式主要分为车身后置和车身底板下置2种,其中底板下置的布置方式能够降低车身重心、提高整车操纵稳定性和优化碰撞传力路径,已经成为电池包布置的主要方式。

3.2 电池包下箱体结构
电池包下箱体作为电池包系统的承载部件,内部结构和布局直接影响电池包的使用寿命。下箱体内部布局与其耐撞结构、加强筋和内部模组隔板设计有关。对于下箱体碰撞结构设计,因道路的复杂性和碰撞形式的多样性,不能保证设计出不可穿透的下箱体结构,国内外学者对电池包箱体碰撞结构进行了相关研究。杨威通过选择不同材料和厚度的铝合金箱体对电池包结构抗压性能和电池局部变形进行验证,结果表明,电池包箱体底板的失效位移与板厚无关。Rawlinson在专利中指出,双层防护板和泡沫夹层板的电池包箱体具有良好的防撞效果。此外,也有学者建立了电池包箱体有限元模型,并对其正面和侧面碰撞的安全性能进行分析,普遍认为下箱体碰撞结构选择吸能的三明治结构和双层结构,能提高电池包下箱体的碰撞安全性。
为避免压缩和冲击变形的破坏,同时满足轻量化设计理念,具有局部加强筋的加强板也受到关注。国内外学者对其进行了研究,如:黄娜对钣金件加强筋结构进行了优化,使支撑板的刚度较大幅度提升;段昀辉等对车身钣金件不同区域加强筋进行优化,得到了加强筋最优设计方案;Afonso等针对变厚度板壳进行优化,得到了加强筋的布局和形貌。电池包箱体设置加强筋,使箱体受力时不易变形,同时固定了电池组阵列,提高抗弯扭强度,改善了其抗失衡能力。加强筋设计时应充分考虑其截面、起筋方向和排布,在保证箱体刚度的前提下,尽可能降低其在电池箱内部的空间占有率。
新能源汽车电池组多为2层或多层排布,电池箱内常设有隔板以实现电池包各层的安装固定。隔板设计时应考虑其与箱体、连接结构间的稳定性,在保证隔板刚度的条件下,尽可能减轻质量。目前电池箱体的内部多以贯通的截面梁和管、管状梁方式布置,多个横梁、纵梁将电池包内部分为多个电池模组的安装区域。部分新能源汽车电池包下壳体内部结构如表3所示。
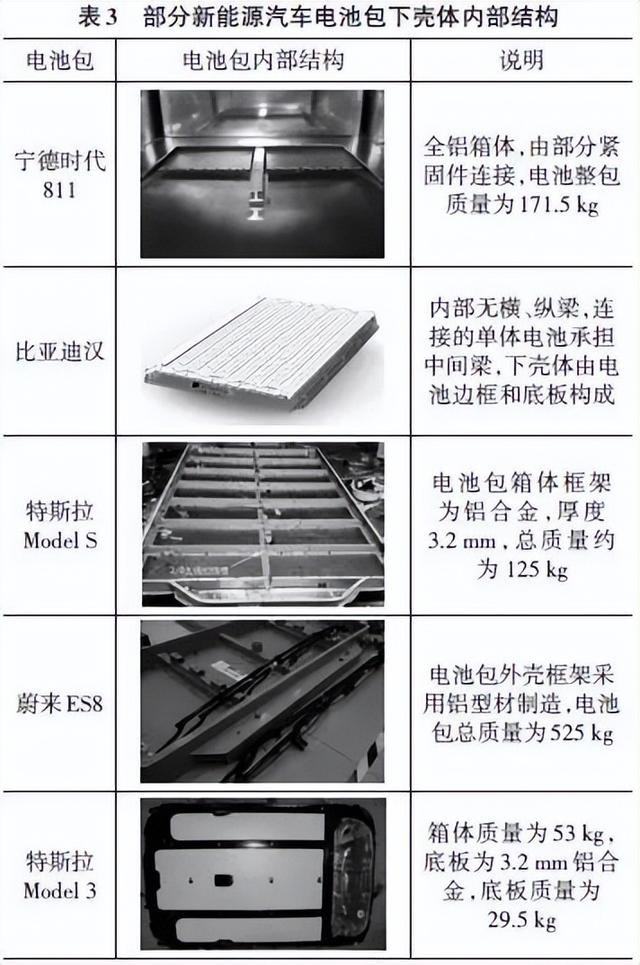
3.3 电池包箱体轻量化优化方法研究
为了在较短时间内开发出性能优良且稳定的产品,研发阶段不仅要使用传统试验技术,还常利用有限元仿真技术,辅助完成产品的优化设计。国内外学者在电池包箱体轻量化仿真优化上也进行了针对性研究,
如:Hartmann等采用有限元优化软件OptiStruct对电动汽车电池包箱体的形貌进行优化设计,成功减小了电池包箱体的壁厚,使整体质量减轻了20%;
Wang等建立了电池包有限元模型,进行多目标拓扑优化,确立了材料的最优分布,使电池包箱体质量减轻了10%;
Kaleg等利用铝合金对电池包板厚进行优化,并得到最佳质量的电池包箱体;LIU等开发了一种碳纤维编织布的优化设计方法,通过多尺度参数优化,在满足性能要求的前提下使得复合材料电池包箱体质量减轻了22%;
张宇等利用CAE有限元分析方法对电池包箱体下板进行形貌优化,使电池箱体结构力学特性更合理,质量减轻了61.39%;陈球胜用高强钢和铝合金对电池包箱体进行材料替换,并对箱体的厚度进行多目标优化,成功使箱体质量减轻了25.5%;兰凤崇等通过多材料并用和优化流程的方法,利用试验设计、模拟拟合和遗传算法优化系统结构,在保证性能的前提下 ,使电池包箱体质量减轻了47.3%。此外,湖南大学也使用CAE技术对电池包箱体不同部位进行优化,实现了不同程度的轻量化效果。
4
电池包箱体制造技术轻量化
制造技术是决定电池包箱体能否商业化的重要途径,电池包箱体的一次成型技术和连接技术也是实现其轻量化的重要手段。从箱体的成型技术和连接技术两方面进行优化,在一定程度上也能减轻电池包的自重。
4.1 电池包箱体成型技术
电池包箱体的成型技术主要根据其选用的材料决定,目前多以铝板和纤维增强材料作为电池包箱体用材料,不同企业采用的成型技术也有所不同。铝板主要的成型技术为冲压铝焊接、挤出铝搅拌摩擦和铸造等。在不改变箱体强度的条件下,特斯拉Model系列和宝马i3利用冲压铝焊接工艺,使箱体质量减轻了40%;大众Golf GTE插电混动版和宝马X5电池包箱体都利用铸造成型工艺制造而成。还有一些新的铝合金成型技术,如上海交通大学开发的铝合金大部件真空压铸技术、北京有色金属研究院的铝合金半固态流变压铸技术,后者的成本只稍高于常规压铸,并能实现35%~48%的轻量化效果,在汽车零部件中的应用十分广泛,预计未来会成为电池包箱体的主要制造工艺。
复合材料成型工艺众多,如热压罐、树脂传递模塑成型(Resin TransferMolding,RTM)、真空导入、注射、挤压和喷射等。生产和制造过程中,可根据零部件特征、成本和选用的复合材料类型选择最合适的制造工艺,目前常采用注射一次成型的方式生产纤维增强复合材料电池包箱体。碳纤维增强复合材料目前只在部分车型中使用,其材料和制造成本下降到一定程度后,碳纤维复合材料箱体将是未来新能源汽车电池包箱体的主流。
4.2 电池包箱体连接技术
目前电池包箱体由纯金属箱体向金属-复合材料混合型箱体过渡,以异种材料的组合为主要形式。异种材料连接成的复合结构的最大优点是抗疲劳性、耐腐蚀性和轻量化性较好,尤其是轻量化方面。不同材料间的主要连接方式为胶接、机械连接和混合连接。
目前新能源汽车箱体以铝材或混合材料为主,多以紧固件连接形式进行固定连接,铝制箱体与车身的连接对稳定性要求较高,主要用搭铁螺栓、铆接并配合加强筋进行连接。在电池包箱体自身连接技术上,国内外学者也进行了研究。
Schmerler等在不损伤纤维材料的情况下,利用胶接等方式对三明治结构电池包箱体各部分实现了良好的连接。赵河林利用钨极惰性气体保护(Tungsten InertGas,TIG)焊对某国产5052铝合金电池包箱体成功完成了密封焊接。徐治勤等利用流钻螺钉(Flow Drill Screw,FDS)工艺对某款铝合金电池包箱体进行连接,实现了铝合金箱体板材间的有效连接。李红等系统分析了国内外电池包箱体连接技术研究成果,并提出了紧固件是目前电池包箱体连接的主要形式,对一些特定材料需采用激光焊接进行密封。异种材料间的连接需要根据其连接部位、刚强度要求有针对性地选择适合的连接方式。
对于电池包箱体与车身的连接形式,各企业采用的方法也不尽相同,目前国内外研究成果较少。以碳纤维箱体为例,箱体与车身的连接处常使用金属接头,接头与材料主体结构层采用胶接辅助粘接,以混合连接的方式进行固定。“机械固定+胶接”混合连接的方式,也可以有效提高轻型构件和车身结构的疲劳强度、扭转刚度和耐撞性,轻量化的同时使得连接具有良好的稳定性。中国的汽车相关企业在电池包箱体和车身的连接工艺上也申请了多项专利。
5
动力电池包的标准和性能评价方法
电动汽车电池包的安全性越来越受到人们的重视,由于电池包的种类繁多,且电动汽车使用环境各异,国内外动力电池包相关标准的内容也各有不同。目前,关于动力电池包的标准主要由欧盟、国际标准化组织、中国、美国和德国等制定。安全性是制约电池包应用的关键因素,各国的标准在安全性评价方法方面都有明确的规定,评价的主要内容围绕机械安全(振动、冲击和跌落等)、环境安全(热冲击和热稳定性)和电气安全(短路和过充放电)3 个方面。中国在2015年相继制定了6项动力电池新标准,其中有3项标准(GB/T 31484、GB/T 31485和 GB/T 31486)不再局限于锂离子电池,而是包含了所有动力电池包的类型。国内外标准对电池包安全性测试的内容如表4所示。
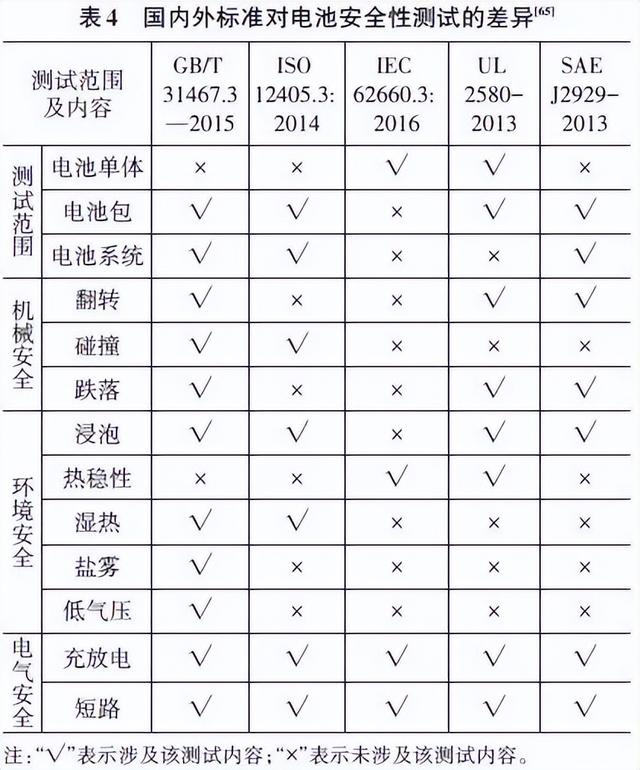
由表4可以看出,国内外标准在测试内容和覆盖范围方面均有所不同,评测的主要对象以电池单体、电池模块和电池包系统为主。在安全性测试方面,中国标准GB/T 31467.3—2015增加了盐雾和低气压测试碰撞测试,中国标准在环境安全性检测评价的内容上要多于国外标准,而欧盟标准IEC 62660.3: 2016和美国标准UL2580-2013在热稳定性方面则有详细说明,特别地,在温升测试中,美国标准 UL 2580-2013还针对电池包外壳和关键零部件对温度的耐受力进行了测试,并对电池包外壳体表面开口的设计规范进行了说明,其他标准则没有相关规定。
此外,国内外标准在动力电池包的性能评价上侧重点各有不同,且都没有提出电池包安全时效性的性能评价方法,故需结合电池应用情况,制定电池包全周期性能评价体系,以满足电动汽车电池包不断发展的需求。
6
结束语
综合国内外电池包箱体所用材料和结构来看,在材料的选择上:若选择金属作为箱体材料,制造工艺非一次成型,需要进行后续焊接加固等步骤,增加了电池包的质量;若选择复合材料,则需要平衡电池包箱体的制造成本、刚强度和疲劳耐久等性能。目前电池包箱体主要以铝合金下箱体和SMC复合材料上盖为主,混合材料箱体结构将是主要的发展趋势。在结构设计上,电池包箱体需考虑空间、密封、散热和碰撞安全性能等因素,同时需要保证电池包箱体上、下结构连接和整个箱体与车身连接的可靠性,综合车身-底盘电池包结构一体化和电池包箱体轻量化所用材料将是两大重要的轻量化发展方向。此外,电池包的性能测试评价的标准应增加整车级别和全生命周期的综合性验证。
文章来源于网络,如有侵权,请联系删除
相关参考
新能源电动汽车电池箱(新能源汽车电池包箱体结构的轻量化研究现状)
...池系统热失控和整车起火爆炸,故动力锂离子电池已成为新能源汽车动力系统领域研究的热点和难点。电池包箱体(壳体)是电池包的主要承载部件,只有箱体的静、动态(刚强度、模态等)稳定,才能保证动力电池不出现滥用...
泡棉胶带在汽车的应用(闭孔发泡硅胶在电池包壳体防潮密封中的应用)
...他防水防潮密封,有广泛的应用。 1、背景介绍 电池包是新能源汽车核心能量源,为整车提供驱动电能,为保护电池包内部
泡棉胶带在汽车的应用(闭孔发泡硅胶在电池包壳体防潮密封中的应用)
...他防水防潮密封,有广泛的应用。 1、背景介绍 电池包是新能源汽车核心能量源,为整车提供驱动电能,为保护电池包内部
整车气密性检测设备(电池箱气密性检测要如何做呢?电池包防水检测有哪些要求?)
电池作为新能源汽车核心能量(电能)来源,是为整车提供驱动所需要的电能,因此需要保护动力电池内部不受灰尘等微小颗粒、雨水等液体的侵蚀,那么电池气密性检测就必须达到一定的防尘防水等级标准,这样才能安全可靠...
开关电源导热硅胶片(轻量化导热硅胶片,新能源汽车电池导热硅胶片)
轻量化导热硅胶片,新能源汽车电池导热硅胶片GLPOLY是一家专注研制导热硅胶片产品的中国公司,是中国导热材料行业最具影响力的新材料开发企业,公司致力于为客户提供精准的导热产品及创新的导热解决方案服务,以满足客...
...汽车轻量化、节能环保需求的铝合金精密压铸件。【深化新能源布局】公司大力开发新能源汽车项目,在电机、电池、电控零件上均有所突破,电驱动壳体、车载充电机壳体、电源转换器、电池盒、逆变器、电驱动轴承、新能源...
...球知名长寿命电池品牌,业内公认的“长寿王”,由著名的新能源产品供
氢电导树脂(电动汽车用胶行业研究:轻量化+热管理双驱动,进口替代趋势形成)
...备质量。汽车自身质量降低,能显著增益节能减排效果:新能源汽车减重10%,对应续航里程可增加5%~10%,并节约15%~20%的电池成本以及20%的日常损
模组控制器(浅析汽车动力电池包的组成、成组技术及成组效率对比)
摘要:本文在概述了汽车动力电池包组成的基础上,重点探讨了动力电池成组对电芯高能量密度、轻量化、结构设、安全、热管理、电气、标准化设计要求的要点,并对动力电池成组效率进行比较。关键词:组成要求效率1.汽车动...
托盘焊接工装设计(一款铝合金液冷电池托盘产品的开发与设计讲解)
电池包作为新能源汽车的主要储能元件,直接影响电动汽车的性能。电池包在使用过程中会产生一定热量,使内部温度升高。若热量来不及散出可能会出现漏液、放气、冒烟等现象,严重时电池发生剧烈燃烧甚至爆炸。因此电池...