水溶性切削液对人体的危害(维懂百科--水溶性切削液)
Posted
篇首语:知识就是力量,时间就是生命。本文由小常识网(cha138.com)小编为大家整理,主要介绍了水溶性切削液对人体的危害(维懂百科--水溶性切削液)相关的知识,希望对你有一定的参考价值。
水溶性切削液对人体的危害(维懂百科--水溶性切削液)
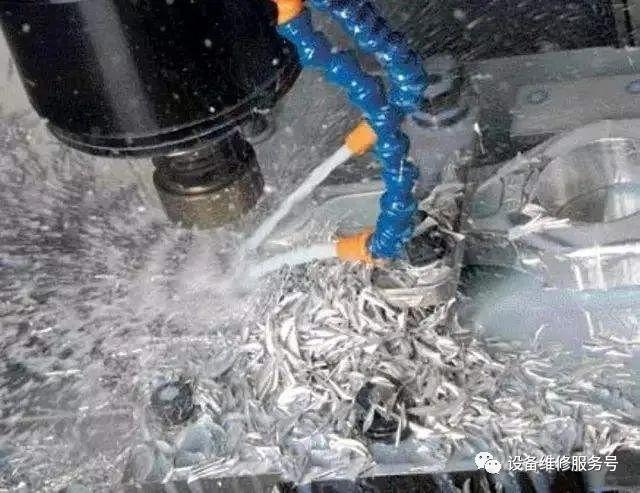
前言
应用上称为全合成、半合成、微乳液的,归为此类,是目前应用最广,用量最大,也是非标订制最普遍的品种。主要是以客户的特殊要求定向开发,在性能与成本上求取一个公约数。
水溶液是以水为主要成分的切削液,因为水的导热性能和冷却效果好,但单纯的水容易使金属生锈,润滑性能差。因此,常在水溶液中加入一定量的添加剂,如防锈添加剂、表面活性物质和油性添加剂等,使其既具有良好的防锈性能,又具有一定的润滑性能。在配制水溶液时,要特别注意水质情况,如果是硬水,必须进行软化处理。
一般而言,水溶液类易起泡,润滑效果不如乳化型切削液。其中全合成型水溶性切削液还相对比较容易伤手。
乳化液类(原液中含有少量水的乳化型切削液)
乳化液是原液基本不含水或含有少量的水(少于5%),使用时用20-30倍的水稀释而成工作液,呈乳白色或半透明状的液体,具有良好的冷却作用。但润滑、防锈性能较差。通常再加入一定量的油性、极压添加剂和防锈添加剂,配制成极压乳化液或防锈乳化液。乳化性产品一般被用在中中-重度切削加工中,如拉削,在加工工艺中会使用到拉刀。
一般而言,乳化型切削液比半合成、全合成、微乳液易发臭。但润滑极压效果会好一些,工作液的乳液稳定性是产品优劣的重要指标。
切削油类(原液与工作液均不含有水的切削纯油)
按国标分类,以润滑为优先考虑的切削液就是切削纯油。切削油的主要成分是矿物油,少数采用动物油或复合油。纯矿物油不能在摩擦界面形成坚固的润滑和防锈作用。纯油含有油溶性功能添加剂,都不可溶于水。大多数的切削油是基于环烷油制成的,为了使其具有更好的可添加剂溶解性。切削油通常被用在钻孔,攻丝,及那些需要高润滑性要求的加工工艺中。
总结
从成本透明性而言,切削纯油>乳化液>水溶液
从使用经济性而言,乳化液>水溶液>切削纯油
从管理难度而言,水溶性>乳化液>切削纯油
水溶性切削液
1.定义
水溶性切削液(water soluble cutting fluid),是由极压剂、防锈剂、矿物油及多种表面活性剂,经科学方法调制而成的新一代半合成微乳型水溶性切削液。
水溶性切削液是介乎全合成切削液与乳化液之间的一种半合成切削液,既有乳化油的润滑性、极压性而且又具备合成切削液的环保性能、优异的清洗性能、使用周期长等性能,同时也具备优越的极压性及良好的消泡性、防锈性。
水溶性切削液适用于钢、铸铁、不锈钢、铜铝及其合金等金属的切削加工,使用周期长;水溶性切削液广泛应用于大型加工中心和自动车床上。当前水溶性切削液的主要设备提供商有美国奎克(castrol)、英国嘉实多(quakerchem)、德国福斯(fuchs)等国际知名品牌。
2.特点
水溶性金属切削液的主要目的:
(1)延长刀具的使用寿命;
(2)保证和提高工件的加工尺寸精度;
(3)改善工件表面的光洁度;
(4)及时排除金属屑,确保切削过程顺利进行;
(5)及时带走切削热,迅速均匀冷却刀具和工件等;
(6)防止机床和工件产生腐蚀和锈蚀;
(7)提高切削加工效率,降低成本。
为实现上述目的,要求水溶性金属切液必须具备下列几方面主要性能:
冷却性能
在金属切削加工过程中,所消耗的能量,绝大部分(90%以上)都转变成切削热,它不但使刀具容易磨损,而且使工件容易产生局部烧伤或发暗,影响工件的表面的加工精度及加工质量。因此,要求水溶性金属切削液必须具有良好的冷却性能。
润滑性能
刀具在切削工件的瞬间,通常承受着极大的切削力作用,水溶性金属切削液良好的润滑性能可以减小刀具前刀面与切屑、后刀面与工件表面之间的摩擦与磨损,延长刀具的使用寿命,从而使工件获得良好的加工精度和粗糙度;更重要的是减少切削过程中产生积屑瘤(即刀瘤)的机会。
清洗性能
金属在切削(或磨削)过程中,油污、细小的切屑、金属粉末和砂轮砂粒等互相粘结,并粘附在工件、刀具和机床上,影响工件的加工质量,降低刀具和砂轮的使用寿命,影响机床的精度。因此,水溶性切削液应具有良好的清洗作用,减少细小的切屑及金属粉末等的粘结以利清洗,同时迅速将细小的切屑及金属粉末等及时冲走。
防锈性能
水溶性金属切削液在使用过程中大部分是水(约占80%-98%),为锈蚀的产生提供了有利的环境,而水溶性金属切削液中的极压剂和某些表面活性剂往往会加剧金属的锈蚀;同时,水溶性金属切削液必须具备一定的防锈性能,使工件在加工过程中和加工后的短时间内不产生锈蚀;同时,水溶性金属切削液良好的防锈性能,也可保证切削液循环系统和机床内部不产生锈蚀及腐蚀现象,起到保养设备的功能。
同时,因为水溶性金属切削液的组成成分中含有如表面活性剂、基础油、油性剂和杀菌剂等,以及其与水混合的应用方式特点,要求水溶性金属切削液还必须具备良好的抗泡/消泡、抗菌性能,以及低毒/无毒性、硬水适应性和气味柔和等特点。
水溶性切削液不同于切削油很重要的一点,是它会引起机床和工件的锈蚀问题。
1.在使用的稀释水中,如含有很多氯化物和硫酸盐,则不仅使防锈性能下降,还会发生腐蚀现象。
2.水溶性切削液在正确的浓度下,是可以防止锈蚀发生的,但浓度降得过低或组织平衡被破坏,防锈性就会下降。防锈性能如果下降,就应补充原液来提高浓度。
3.磨削中常用浸硫砂轮和含有冰晶石的砂轮。随着磨粒的脱落,硫和氟化物会混入切削液中,促使防锈成分不断消失,加速防锈性能的下降。这里虽然可通过原液或防锈剂的补充来维持防锈性,但根本上还应经常有效地清除磨削中落入切削液里的各种粉粒。
4.使用水溶性切削液加工铝合金工件时,工件表面易于出现白锈。其原因之一是切削液中积蓄了较多的氯离子。由于目前还没有有效防止白锈的添加剂,所以这时应更换切削液,以减少氯化物。
3.维护方案
一、 切削液的管理
浓度管理
正确维护好冷却液的使用浓度将会给冷却液带来长的使用寿命及良好的加工性能。使用合适的浓度是非常重要的,太高的浓度会给操作工人带来皮肤刺激,太低的浓度又会造成细菌的繁殖,工件加工质量会下降,刀具寿命会缩短。检测浓度最简单且有效的方法是采用折光仪。只需要少量的工作液滴在折光仪的面板上,将折光仪对准亮光的地方就可以读出折光读数。折光读数乘上产品特有的折光系数就是工作液的浓度。有时由于杂油的混入读数的分界线会不太清楚,这时需要估计一下读数。
冷却液的浓度直接关系到冷却液各项性能的发挥,如浓度异常,则可能会发生以下问题:浓度过高时,出现泡沫问题,皮肤刺激性增强,对机床油漆面产生影响,机床及机床周围容易形成污垢;浓度过低时,切削性能不佳(因润滑性不够导致工具寿命、加工精度和加工光洁度的下降),工件、机床和切屑等生锈,耐腐败性降低(冷却液使用寿命缩短)。
水硬度
通常金属加工液的生产厂家所给出的产品防锈性能是在用中等硬度水配制并以标准试验方法测得的结果。水的硬度由溶解于水中的矿物质的含量所决定,硬度太高易导致出现乳液不稳定现象,容易对金属造成腐蚀。通过滴定或硬度试纸可以很容易测得水的硬度。
由于水分是不断蒸发的,而工作液中的矿物质成分、添加剂或油分不会蒸发,所以工作液的浓度及组分是不断变化的。这个变化的大小与使用温度及工作液的使用频率有关。金属切屑及加工零件的带出同样会影响冷却液的浓度变化,每次加水都会带来矿物质的累积,对稀释水的水质的具体要求如表所示。由于这些盐分会带来对工件及机床部件的腐蚀,因此对工作浓度的要求会随使用时间的延长而相应增加,以用于抵抗盐分增加所导致抗腐性能的降低。溶入到工作液中的盐分是很难被去除的,只有两个办法可以采用,提高冷却液的防腐能力,或是将冷却液换成新液。
微生物管理
金属加工液一旦与水混合后就会不可避免地受到微生物的攻击。自来水或者雨水中都存在有各种细菌、真菌、霉菌和酵母菌等,这些菌种可以在温暖的化学物质存在的环境下快速生长。空气中细菌的传布也是存在的。冷却液中通常包含有抗菌的组分,这些组分在保持有一定水平的情况下可以有效地抵抗微生物的侵害,但是这些组分在使用的过程中会消耗。
另一种控制细菌的方法是生物稳定型,就是允许一定细菌的存在但不让其过度繁殖,比如将细菌的数量控制在1×105个/ml以下。乳化液通常容易被细菌攻击,半合成液更容易被真菌所攻击。细菌的攻击导致表面活性剂的消耗从而影响乳液的稳定性,最终使得油水分离。细菌的生长分解出更多的酸性物质降低了工作液的pH值,还会导致腐蚀及皮肤过敏的发生。如果冷却液箱中总是覆盖一层杂油就会促使厌氧菌的生长。厌氧菌将硫转化成硫化氢气体,闻起来就是一股臭鸡蛋味。
通常工厂工作一周后会放两天假,这个时候就需要尽量将冷却液箱中的浮油从液面撇除。同时也可以添加适当的后处理用杀菌剂来控制细菌的生长,但值得注意的是要掌握好添加量,加得太多会引起皮肤不适。杀菌剂大都是甲醛释放型,添加时甲醛在工作液中的含量控制在800~2000ppm之间。大于2000ppm皮肤过敏的可能性大大增加,小于800ppm起不到杀菌作用。
真菌、霉菌或酵母菌繁殖后会形成粘稠的皮状物,最终这些皮状物覆盖在液面以及机床内部并堵塞滤网及管道。这时甚至加入杀菌剂也不能完全杀灭,因为杀菌剂很难穿透这层皮膜。只能通过物理方法来清除。一旦清理完后应当立即加入杀真菌剂,不然真菌还会很快生长出来。通常可以采用测菌片进行细菌检测。
冷却液中繁殖的微生物主要是存在于尘埃、土壤中的细菌、酵母菌之类。 事实上,微生物的混入是不可避免的,因此,为防止冷却液腐败,应该在冷却液的细菌数超过1×105个/ml或真菌数超过1×102个/ml时,立即添加杀细菌剂或杀真菌剂处理。 冷却液中的细菌、真菌可以用细菌、真菌测定盒测定。 测定结果细菌在1×103个/ml以下,真菌0为理想。 用户也可以根据经验定期添加杀菌剂,以确保冷却液的使用寿命。
pH值管理
pH值降低是造成冷却液腐败、工件生锈的直接原因之一,如图3所示。因此,经常测定冷却液的pH值,并使其保持在指标值范围之内,可将有效地防止冷却液的腐败和工件、设备的锈蚀现象。如发现pH值降低现象,首先进行浓度检测,如浓度正常,则添加pH值向上剂;如浓度偏低,则首先补充原液,校正浓度;如浓度校正后pH值仍偏低,可以添加好富顿pH调整剂以提高pH值。
杂油及管理
通常冷却液均具有一定的抗杂油能力,但大量杂油(如导轨油、液压油等)的混入将大大加剧冷却液的劣化速度,导致冷却液的分离、腐败等现象。因此,必须安装撇油器以及时除去混入的杂油,并经常记录润滑油的补给量,及时发现、修补泄露处,使杂油混入量控制在最小限度,这将有效地延长冷却液的使用寿命,从而降低使用成本。
由于新生的切屑具有较强的反应活性,会过多地消耗冷却液的有效成分,因此,及时清除产生的切屑(必须安装磁性过滤器或其他过滤设备),也是维持冷却液各项性能不受影响的重要手段。
二、 常规切削液维护流程
(1)新液配制
混配液:如果原液的自身的乳化性能好,只要把一定量的原液加入到稀释用水中,充分搅拌均匀即可得到均匀的乳化液,需要注意的是,配制乳化液时,需要将原液加入到稀释水中,如果反其道而行之,将稀释水加入到原液之中,在有些特殊情况下(如在较低温度下),可能生成胶状物质,之后很难再溶解开来。
在具体的工业应用中,一般是先将切削液原液通过混配器混配成一个较高浓度的混配液。在没有混配器的条件下,可以在一个容器中加入一定量的水,再加入原液,需注意加入原液时务必、稳流且缓慢,边加入边用工具搅拌,使原液充分地与水混合。切记,不可将水加入原液中,只能是将原液加入水中。
微乳液和全合成液的配制,由于其本身是水溶性的,液态的原液本身就含有一定量的水,较易溶解,稀释过程较简单,但也要遵循将原液加注到稀释用水中的原则。
混配液加注:混配液制备好以后,根据系统要求浓度和容量计算出混配液的加注量,再将混配液加注到液箱中。加注前一定要保证液箱清洗干净,有条件的情况下,可以用专用机床清洗剂或低浓度的切削液进行清洗。
液体调整:加注的混配液浓度较高,不能达到容积要求,这时需要补水。补充的水可直接加入到液箱中的混配液中,以达到液箱容积要求为止。切削液在调整时,要进行系统液体的循环运行,使液体处于流动状态,以使切削液混合均匀。这个循环过程的时间要根据系统的循环流量确定,一般不少于2h。
(2)日常加注
在切削液的使用过程中,浓度会逐渐下降,需要定期进行浓度检测,检测方法一般是折光法或滴定法,依据检测的浓度结果与要求的浓度控制要求对比,计算出需要补加的原液的量,再折合成混配液的量,做出补加计划进行加注。
(3)系统清理
当切削液使用到一定时间以后,液体中的杂质含量会增加,主要是加工过程中产生的细小颗粒、切削液本身的生成物、导轨油和液压油等的泄漏及水中带入成分的沉积等。这些杂质或悬浮在液体中,或沉积到箱底、箱壁或在机床的内表面。特别是悬浮在液体中的杂质,能影响到液体的化学指标,影响到切削液的润滑性、清洗性和防锈性,沉积的杂质能引起细菌和真菌的孳生。大颗粒的杂质会影响到工件的表面粗糙度。现在的切削液系统,一般都带有液体净化装置,如网式过滤、沉淀、离心分离、磁分离和网布过滤等。但其中的细小颗粒和悬浮杂质不能全部净化去除,而在液体中积累。所以要定期进行系统的清理,以去除系统的杂质。
(4)换液
当切削液使用到规定寿命后,冷却、润滑、清洗和防腐性能下降,现场应用中可能发生如下情况:切削液的外观变化,有变黄、变黑的,也有变混浊的,总的说液体失去其本来的光泽。切削液各种控制指标波动大:浓度变动大,pH值下降,细菌和真菌高发,防锈性下降,若进行攻丝转矩或四球试验,试验结果可能发生突变。加注需求量明显增加,加注量增大而相应指标不同步变化。加工质量变化,特别是工件表面粗糙度和刀具寿命发生变化。
三、 切削液的消耗
(1)加工中的切屑带出。在加工过程中,切屑的排出依赖于刮屑链、滤纸和滤布等,在这个过程中,切削液会被带出到切屑箱。这部分液体从切屑中沥出后一般是按废液处理。对于集中冷却的大系统,也有设计专用的回用装置,通过净化处理后返回到系统中应用。
(2)加工中的蒸发。加工过程中的切削液,由于加工热量、液体流动和加压泵等原因,温度升高,使切削液蒸发加快,特别是利用了烟雾收集器后,汽化的切削液会被当作加工烟雾排出。
(3)加工中的有效成分消耗。刀具与工件作用时,作用部位产生局部高温,切削液中的相关成分,如有些极压添加剂等被消耗,产生切削液浓度的下降。
(4)到使用寿命后的换液。切削液寿命到期前要进行切削液的更换,是集中消耗。原用液体全部作为废液处理,系统排空后完全配加新的切削液。
(5)切削液原液的消耗量。以一条年产量为20万台的发动机缸盖生产线的统计为例,每年更换一次冷却液的原液消耗为4?200kg,每年加注的混配液中的原液量为34?440kg。可以看出,主要的切削液原液消耗是日常加工过程消耗,而不是换液消耗。换液过程消耗量只占总消耗量的11%。
四、 切削液性能变化
(1)切削液使用寿命确定。项目期,依据切削液供应商的经验推荐确定。正常生产阶段,依据液体状态变化趋势、生产产量和生产停机时间确定。优化阶段,依据历史经验、日常检测分析和加工工件变化状态等,合理优化切削液的更换周期。
(2)切削液的性能变化可分为几个阶段。一般按切削液使用时间顺序,将切削液的性能变化分为四个阶段:新液阶段、正常维护阶段、清理后维护阶段和换液前维护阶段。清理时机,一般在使用寿命一半的时间;换液前维护阶段,有时需要适当增加切削液的浓度,如整体提高控制浓度1%或按上限控制等;在加工条件较差的情况下,如高温、高湿等环境中,在换液前维护阶段还要增加防锈剂、杀菌剂和pH调整剂等添加剂。
五、切削液统筹维护方案
1. 基本原理
当一个系统的切削液使用到一定的时间(如使用寿命的一半)后,将其做为补加液分加到其他系统,而本系统配制新液。这样既保证了各系统的添加混配液良好,也使各系统都在一定的时间之内换液。前提条件:一是冷却液抗菌性和稳定性良好,二是切削液的消耗主要是日常添加混配液,换液消耗原液量占总消耗量的比例小于20%,结果是液体随着使用过程消耗掉,而不产生集中排放的废液。
2. 技术研究的特点
在保证常规切削液性能和有效的过滤技术的基础之上,进行切削液应用过程的研究。在切削液的应用过程中,切削液主要是被加工过程消耗掉,而没有被集中排放掉。
3. 实施过程
(1)划分切削液系统统筹维护单元。统筹维护单元划分原则:切削液型号相同、切削液系统容积相近、加工工件材质相同、设备的位置相对集中。
(2)实施步骤。以每个统筹维护单元为维护单位。对于每一个切削液系统,使用到一定时间后,进行切削液的更换。原用液不排至污水站,而是进行净化处理,之后,作为混配液加注到同一维护单元的其它系统中,而本切削液系统配制新的切削液。
清洗系统用液,可以配制一个低浓度的切削液,如1%~2%切削液。清洗后也经过净化处理,与原用切削液都作为混配液补加到同一维护单元的其他它系统中。清洗过程使用低浓度切削液是为了增加清洗效果且增加防锈性、降低泡沫的产生。清洗过程不加入机床清洗剂。
冷却液和清洗后的液体的净化处理,一般可采用如下方法:①沉降法。在容器中放置一定时间,撇除上部漂浮杂质,去除底部颗粒杂质。②离心法:去除密度大的颗粒和密度小的油类。③过滤法。用滤纸或滤袋过滤其大颗粒的杂质。
4. 效果评价
① 切削液技术指标评价:浓度每天检测,指标变化平稳;pH每天检测,指标变化平稳;抗菌性每月检测,没有细菌和真菌的发生;防锈性每月检测,指标平稳,在控制范围之内;硬度每周检测,指标有增加趋势,原因是添加的自来水硬度较高,但不影响切削液性能。若使用RO水,硬度指标会更加平稳。
②切削液成本费用评价。按换液费用所占比例计算,切削液的费用节约约为10%。
③废液减排评价。按切削液的换液过程统计,每次换液清理时,会有较脏废液的排放,如液体表面含有浮油的液、液箱底部沉积物中的液以及进行切削液再生处理时排出的废油液,这部分废液约占被处理液的10%~20%,即换液过程排放的废液减少80%。
********************************************
内容参考:机械论坛
本期编辑:Johnxing
版权声明:设备维修服务号尊重版权并感谢每一位作者的辛苦付出与创作;除无法溯源的文章,我们均在文末备注了来源;如文章视频、图片、文字涉及版权问题,请第一时间联系我们,我们将立即删除内容!
相关参考
前言 应用上称为全合成、半合成、微乳液的,归为此类,是目前应用最广,用量最大,也是非标订制最普遍的品种。主要是以客户的特殊要求定向开发,在性能与成本上求取一个公约数。 水溶液是以水为主要成分的切削液,因...
前言 应用上称为全合成、半合成、微乳液的,归为此类,是目前应用最广,用量最大,也是非标订制最普遍的品种。主要是以客户的特殊要求定向开发,在性能与成本上求取一个公约数。 水溶液是以水为主要成分的切削液,因...
油性切削油使用过程中有异味(佳和三英:切削液的废液处理方法)
...竟,保护环境就是保护我们自己)。今天我们一起来看看水溶性(水基)切削液和非水溶性(油基
油性切削油使用过程中有异味(佳和三英:切削液的废液处理方法)
...竟,保护环境就是保护我们自己)。今天我们一起来看看水溶性(水基)切削液和非水溶性(油基
水溶性切削液对皮肤的影响(切削油的分类与应用详解,新手必看)
...在金属加工作业中,切削油基本上可区分为油性切削油、水溶性切削油、合成切削液三大类。一、油性切削油油性切削油一般多以低粘度矿物油为基质,再与其它添加剂混合制成,使用时不需要再稀释。矿物油有许多不同的种类...
水溶性切削液和非水溶性切削液(水基切削液和油基切削液有哪些区别差异)
水基切削液和油基切削液的差异表现在四个方面:理化功能上的差异、加工功能上的差异、经济性上的差异、环卫功能上的差异。理化功能的差异水性切削液冷却功能和清洗功能较好。这是因为水比油的比热容和热导率高。水性...
大多数的数控机床都是尽可能以最安全的方式进行专门设计的,但是,因火灾引起机床损坏,会给加工车间造成巨大的损失,特别是当一台机床处于自动化作业或无人化操作时,其发生火灾的风险更高,即使能够迅速地检测或扑...
水溶性切削油是用来冷却和润滑刀具和加工件的工业用液体,是由多种超强功能助剂经科学复合配伍而成,同时具备良好的冷却性能、润滑性能、防锈性能、除油清洗功能、防腐功能、易稀释特点。水溶性切削油目前广泛使用在...
比尔水溶性切削液(盘点美国FDA批准的7款经典抗病毒药物)
盘点美国FDA批准的7款经典抗病毒药物来源:博药/青梅过去的很多年里,研究人员一直在开发有效的抗病毒疗法。尽管很多早期的尝试是无效的,甚至走了一些弯路。VanRooyen和Rhodes在1946年出版的《人类的病毒性疾病》中提出了对...
...一部分人消化不了,本期小编给大家分享一款环保长效型水溶性切削液,内容会比较枯燥,希望大家在工作的闲余时间能静下心来一起好好研究学习。《分享一款环保长效型水溶性切削液》环保长效型水溶性切削液特性:本品具...